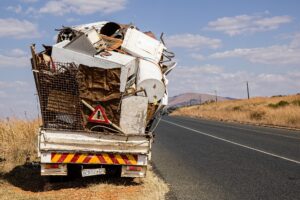
As metal demand soars, can recycling keep net zero goals on track?
BIRMINGHAM, England – At a metal recycling facility in central England, thousands of tons of shredded scrap from cars to construction debris arrive daily to be processed into individual materials and sold.
A mixture of metals, plastics and other materials are sent through an elaborate maze of more than 100 conveyor belt systems where they are further separated in several different ways – from floatation in water to using magnets and robots.
These are just a few of the new technologies utilized by European Metal Recycling (EMR) at the site in Oldbury – a town near the city of Birmingham – as the global company strives not only to make its processes more efficient and profitable but also to do its bit for the environment.
Having started out eight decades ago with one scrapyard, the family-owned multinational firm has now set its sights on the difference it can make in the global green transition, by reducing the need to mine and refine metals.
“You sit there with some pride that you’re making products that have an impact,” said EMR chief executive Chris Sheppard.
“The need to move the world to net zero and ‘nature positive’ is effectively going to require something like the green industrial revolution,” he said.
As demand rises for clean technologies such as electric cars and solar panels, concerns about the environmental impacts of mining and producing the required metals are growing, from damage to biodiversity to rising emissions.
Recycling will prove ever more important as the global race to secure critical minerals heats up, insiders say, and as countries seek a secure supply for crucial metals while also trying to reduce the carbon footprint of their production.
In Europe, for example, 40% to 75% of the clean-energy-related metals needed for products like electric vehicles and wind turbines could be sourced through recycling by 2050 if the continent boosts investment in recycling and makes it more efficient, industry group Eurometaux said last year.
Meanwhile, production of steel – the world’s most widely used metal – is responsible for between 7-9% of the global carbon dioxide emissions that are the primary driver of climate change, according to the World Steel Association.
Using one ton of recycled steel instead of creating new steel avoids 1.5 tons of CO2 emissions, as well as mining 1.4 tons of iron ore, 740 kg of coal and 120 kg of limestone, according to Bellona, an environmental NGO.
However, the last comprehensive research into metal recycling rates – published in 2011 in the Journal of Industrial Ecology – found that only 18 out of 60 metals studied had global recycling rates above 50%.
Its lead author Thomas Graedel, an industrial ecologist at Yale University, said recycling metals has a “very important and underappreciated” part to play in the global green transition.
“We do very complicated things to get these materials into play in the first place,” he said. “Often we use them once and, in one way or another, they’re lost to technology.”
MODERN MATERIALS
Founded in the 1940s by Mr. Sheppard’s great-grandmother after she left wartime London and moved to northern England, EMR now has about 160 sites across the United States and Europe and had a turnover of about 4.7 billion pounds ($5.7 billion) in 2021.
As firms such as EMR seek to grow, a major challenge is the nature of modern materials used in products from smartphones to cars, because of how hard they are to break down and recycle.
Mr. Graedel of Yale cited a 2021 study from the Massachusetts Institute of Technology and US carmaker Ford that found that typical modern cars include 76 different chemical elements.
“I doubt that automobile designers have ever taken a trip to an auto recycling center,” he said.
“Maybe we don’t need to have the very best performance if the trade-off is more climate impact.”
EMR is investing in research aimed at recovering as many materials as possible, meaning the company can generate more profit while putting less waste into landfills – a practice that is costly and harmful for the environment.
“Everything we’re trying to do is to minimize the environmental impact,” said Andy Goodyer, general manager at EMR Oldbury.
Sheppard said the company is also in discussions with manufacturers – such as designers at car companies – to discuss how their products might be formulated in a way that ultimately makes them more straightforward to recycle.
“If they designed the cars with a view to the end of life … you’d be able to recycle them much easier,” he said.
END OF LIFE
Recycling processes for traditional metals like copper and aluminum are more established than those for metals required for the energy transition such as lithium and ‘rare earth’ metals, according to the International Energy Agency (IEA).
Rare earth metals are used in low concentrations to make hi-tech devices – such as neodymium used to make powerful magnets for products like electric vehicles and wind turbines.
Many of these metals are hard to separate from surrounding materials and require new recycling technologies. Often there is a lack of information about how much of each material is used in products and where it is located, experts say.
Luca Ciacci, an industrial chemistry expert at Italy’s University of Bologna, said new techniques like material flow analysis can track the journey of a single element from extraction through production, use, and to the end of its life.
“So in this way we can get a reliable estimate of how much material is available for recycling and where it is,” he said.
These are “fundamental questions” for the development of the recycling industry, Mr. Ciacci added.
Experts also say recycling technologies and expertise need to be developed in the places where products reach their end of life, which is often on another continent – far from where they were built and where people understand how they were assembled.
“We need to get competent workers in recycling centers where products end up being used,” said Mr. Graedel from Yale.
“It is quite uneconomical and inefficient to send products around the world to be recycled.”
GREEN PREMIUMS
In the short-term, recycling will play only a minor role in meeting demand for some metals like lithium, as products containing them – such as lithium-ion batteries in electric vehicles – are still early in their life-cycle, according to Jamie Speirs, an energy researcher at Imperial College London.
Speirs said strong government regulations can ensure recycling infrastructure develops in the meantime.
He gave the example of lead, which has some of the highest rates of recycling among metals due to regulations globally designed to stem health concerns around lead-acid batteries.
Analysts say another key driver of recycling growth is the prices companies such as EMR can command for their recycled materials, and the prices paid to those supplying scrap.
“It will come to you in greater volumes if the price is high,” said Mr. Sheppard.
EMR anticipates that green premiums will mean that recycled metals become cheaper – and ultimately more profitable for companies – than producing virgin materials, he explained.
“It’s really as simple as that,” he added. – Reuters